IEEE 1019-2013 pdf download.IEEE Recommended Practice for Specifying Electric Submersible Pump Cable—Polypropylene Insulation
5.2 Construction
5.2.1 Round design The three insulated conductors should be cabled around a centrally located filler that provides blockage. The conductors should be cabled with a left-hand lay having a maximum length of lay 35 times the individual conductor diameter. A jacket should be extruded over a cable core consisting of three insulated conductors and a central filler. The jacket should be extruded to fill all interstices. The average wall thickness should be 1.5 mm (0.060 in), and the minimum thickness at any point should be no less than 1.2 mm (0.048 in). T
he outer surface of the jacket should have splines. These splines are not considered part of the specified wall; splines are provided for grip of the overlying armor. The jacket should separate cleanly from the underlying components.
5.2.2 Flat design
Each insulated conductor should be individually jacketed. Splines are not required on the jacket. The jacket should separate cleanly from the underlying surface. Additional constraining coverings may be applied over the insulation or jacket. They may be extruded, wrapped, and/or woven type materials. For flat cable with additional constraining coverings, the average jacket wall thickness should be 1.3 mm (0.050 in). The minimum jacket thickness at any point should be no less than 1.0 mm (0.040 in).
For flat cable without additional constraining covering, the average jacket wall thickness should be 1.5 mm (0.060 in). The minimum jacket thickness at any point should be no less than 1.2 mm (0.048 in).
6. Armor
6.1 Material
6.1.1 Size The thickness of the steel strip for round cable constructions, before galvanizing, should have a nominal thickness of 0.64 mm (0.025 in).
The minimum wall thickness at any point should be no less than 0.56 mm (0.022 in). The thickness of the steel strip for flat cable constructions, before galvanizing, should have a nominal thickness of 0.51 mm (0.020 in). The minimum wall thickness at any point should be no less than 0.43 mm (0.017 in). The typical width of the steel strip is 12.7 mm (0.500 in) and should be no more than 19.1 mm (0.750 in) before forming.
6.1.2 Coating The steel strip should be zinc-coated after slitting. The coating should be applied to all surfaces by the hot- dip galvanizing process.
6.1.3 Tensile strength and elongation The zinc-coated strip should have a tensile strength of not less than 275 MPa (40 000 psi) elongation of not less than 10% in 25 cm (10 in). All tests should be performed in accordance with applicable portions of ANSI/ICEA S‐96‐659/NEMA WC71, before application of the strip to the cable.
6.1.4 Weight of zinc coating
The weight of zinc coating should be determined before application of the strip to the cable. The strip should have a minimum coating weight of 110 g/m 2 (0.35 oz/ft 2 ) of exposed surface. The weight of the coating should be determined in accordance with the method described in ASTM A90. The zinc-coated strip should not exceed the bare-metal strip thickness by more than 20% at any point.
6.1.5 Adherence of coating
The zinc coating should remain adherent without flaking or spalling when tested in accordance with applicable portions of ANSI/ICEA S‐96‐659/NEMA WC71.
6.1.6 Armor for harsh environments Thicker steel strip can be provided. Heavier Type II galvanizing may be used as per ASTM A90. For extremely corrosive environments, stainless steel (316L) or other metal alloys are available.
6.2 Construction
6.2.1 Round cable
The armor strip should be applied over the cable core with sufficient tightness to compress the jacket splines to provide sufficient mechanical strength to maintain the integrity of the cable in vertical installation. The strip should be helically applied and formed in such a manner as to be interlocked. The armor should withstand a seven times overall diameter bend radius without separation of adjacent turns.
6.2.2 Flat cable
The construction should consist of the three-phase conductors laid in parallel. The armor strip should be applied over the insulated conductors with sufficient tightness to fit snugly. The armor strip should be helically wrapped and formed in an overlapped manner. The assembly should withstand a bend that is seven times the major axis of the cable. The armor overlap should not open up between adjacent turns. The direction of bend should be in the normal direction of cable spooling.IEEE 1019 pdf download.IEEE 1019-2013 pdf download
IEEE 1019-2013 pdf download
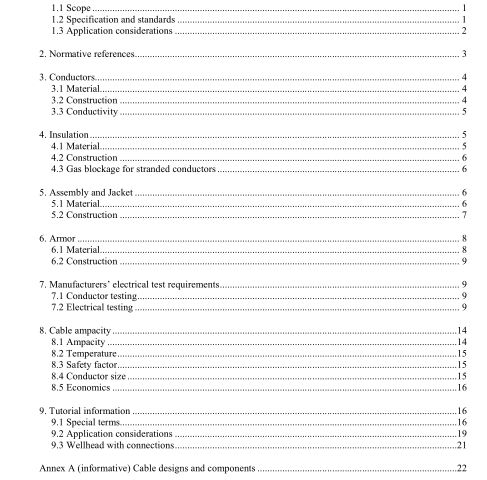
Leave a Reply