IEEE 1017.3-2021 pdf download.IEEE Recommended Practce for Specifying Electric Submersible Pump Cable—Polypropylene Insulaton
5. Insulation
5.1 Material
Insulation should be a thermoplastic polypropylene meeting the properties shown in Table 3 when tested in accordance with ICEA S-61–402/NEMA WC5, Section 6, except that pull rate should be 5.08 cm/min (2.0 in/min). The polypropylene should be copper stabilized. Aging tests should be conducted with the copper conductor in place.
a For special-purpose compound designs (e.g., high modulus compounds), deviations from the tabulated tensile and elongation minimum can be made and should be as agreed upon between customer and supplier.
5.2 Gas blockage for stranded conductors A 30 cm (12 in) specimen of insulated conductor removed from finished cable should be subjected to a 0.03 MPa (5 psi) differential air pressure for a period of 1 h at 25 °C (77 °F).
The sample ends should be cut off flush with a fine-toothed saw blade, and one end of the sample should have a short section of clear flexible plastic tubing slid over the insulation to enable the specimen to be pressurized. The tubing should be attached in place with a small hose clamp [minimum width of binding collar equals 6.4 mm (0.250 in)]. The clamp should be tightened with minimum torque to prevent leakage. The opposite end of the sample should be left submerged in water. No air bubbles should be detected at the submerged end of the cable during the test period.
5.3 Construction
The insulation should be extruded on the conductor with thicknesses as specified in 5.3.1 and 5.3.2.
5.3.1 Cables without metallic barrier For 3 kV rated cable, average insulation wall thickness should be 1.9 mm (0.075 in) or more. The insulation minimum wall thickness should not be less than 1.7 mm (0.068 in) at any point. For 5 kV rated cable, the insulation average wall thickness should be 2.3 mm (0.090 in) or more. The insulation minimum wall thickness should not be less than 2.1 mm (0.081 in) at any point. For 8 kV rated cable, the insulation average wall thickness should be 2.92 mm (115 mil). The insulation wall thickness should not be less than 2.63 mm (0.104 in) at any point.
5.3.2 Cables with metallic barrier For 5 kV rated cable, the insulation average wall thickness should be 1.9 mm (0.075 in) or more. The insulation minimum wall thickness should not be less than 1.7 mm (0.068 in) at any point. For 8 kV rated systems, average wall thickness should be 2.29 mm (90 mil) or more. The insulation minimum wall thickness should not be less than 2.06 mm (0.081 in). Considerations other than voltage stress impact the thickness of insulation.
6. Barrier (optional)
6.1 Material At the option of the purchaser, each insulated conductor could have additional constraining coverings used for fluid protection and hoop strength. These additional coverings may be extruded fluoropolymers, wrapped tapes, or tape and woven braid.
6.2 Flat cable with lead sheath Each insulated conductor should have a lead sheath extruded over the insulation. The average wall thickness should be 1.0 mm (0.040 in), with a minimum thickness of 0.8 mm (0.032 in).
6.3 Flat cable with metallic (nonlead) barrier Each insulated conductor should have a seam-welded metallic tubing applied over the insulation. The thickness of the metallic sheath may vary from 0.5 mm (0.029 in) to 2.5 mm (0.099 in), dependent on the metal used and the specific application requirements.
7. Assembly and jacket
7.1 Material The typical jacket is an oil-resistant thermosetting nitrile rubber meeting the properties shown in Table 4 when tested in accordance with ASTM D412.
An alternative jacket material used in high water cut, low-temperature applications is polyethylene. Cables using thermoplastic polyethylene as a jacket have an upper conductor temperature limit of 80 °C (176 °F).
Additionally, in harsher well environments, the use of more specialized polymeric materials may be used to meet certain well conditions.
7.2 Construction
7.2.1 Round cable
The three insulated conductors, with or without metallic barriers, should be cabled around a centrally located filler that provides blockage. The conductors should be cabled with a left-hand lay having a maximum length of lay 35 times the individual insulated conductor diameter.IEEE 1017.3 pdf download.IEEE 1017.3-2021 pdf download
IEEE 1017.3-2021 pdf download
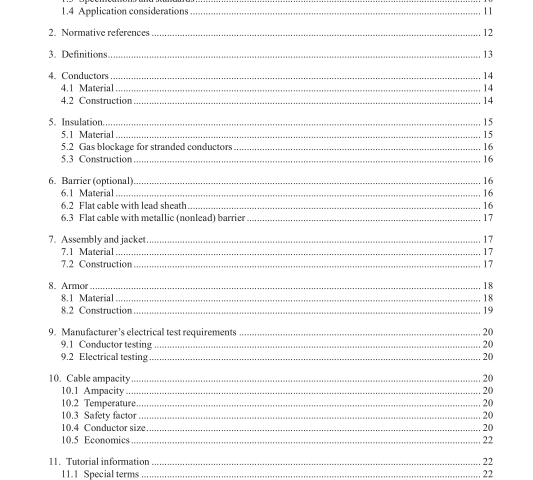
Leave a Reply