IEEE 114-2001 pdf download.IEEE Standard Test Procedure for Single-Phase Induction Motors
Common sources of noise are
a) Inductive or electrostatic coupling of signal leads to power systems;
b) Common impedance coupling or ground loops;
c) Inadequate common mode rejection; and
d) Conducted interference from the power line.
Good practice requires the use of shielded twisted pairs for signal leads, grounding the shield at only one point, and keeping signal cables as far away as possible from power cables.
All exposed metal parts of instruments should be grounded for safety. Instrument calibration requirements are similar to those of nonelectronic instruments. When suitable auto- matic data acquisition systems or high-speed recorders are available, they may be used.
Further information regarding the use of instruments is given in IEEE Std 120-1989.
7 4.1.1 Instrument transformers When current and potential instrument transformers are used, corrections shall be made for ratio errors in voltage and current measurements and for ratio and phase angle errors in power measurements.
The use of instrument transformers shall be avoided if possible (see IEEE Std 120-1989).
The errors of the instrument transformers used shall not be greater the 0.5%.
4.2 Power supply
The power supply voltage shall closely approach a sinusoidal waveform. The voltage waveform deviation factor, as defined in IEEE 100 , shall not exceed 10%. The frequency shall be maintained within ± 0.5% of the value required for the test being conducted, unless otherwise specified. Any departure from the assumed frequency directly affects the efficiency. For a determination of efficiency, the average frequency shall be within ± 0.1% of the required test value.
4.2.1 Frequency stability
Rapid changes in frequency cannot be tolerated in input-output tests because such changes in frequency cause changes in speed and the variations are transmitted to the output-measuring device. Variations in fre- quency during a test shall not exceed 0.33% of the average frequency.
5. Measurements
5.1 Electrical measurements
5.1.1 RMS quantities
All voltage and current measurements are rms values, unless otherwise indicated.
5.1.2 Voltage
The line voltage shall be measured with signal leads connected to the motor terminals whenever possible. If local conditions will not permit such connections, the error introduced shall be evaluated and the readings hall be corrected.
Means should be provided whereby the voltage can be adjusted to the desired value.
This control can be effected by the use of a continuously variable transformer or auto-transformer, by an nduction regulator, or by a controlled motor-generator set.
5.1.3 Current
The line current shall be measured by an ammeter or current transducer. The preferred arrangement of eters is shown by the circuit diagram in Figure 1.
5.1.4 Power
A single-phase wattmeter or power transducer shall be used. The total watts read on the wattmeter, which shall be connected according to 6.1.1, shall be reduced by the amount of the power lost in the voltage circuit of the instruments. Where a properly selected power transducer is used, the transducer loss shall be shown to be negligible.
5.1.5 Resistance
The procedures given in IEEE Std 118-1978
should be used to obtain dc resistance measurements of the stator.
5.1.5.1 Reference ambient temperature
All performance determinations should be corrected to an ambient temperature of 25°C.
5.1.5.1.1 Correction to a specified temperature
5.2 Mechanical measurements
5.2.1 Torque The torque may be measured by dynamometer, with a brake or beam, with a rotating-shaft torque sensor, or by stator reaction.
5.2.2 Rotational speed The instrumentation used to measure rotational speed shall not have an error greater than ± 1.0 r/min.
5.2.2.1 Stroboscopic methods
Stroboscopic methods are recommended when a motor of approximately 40 W or less is tested, due to the load added by the tachometer.
Either an electronic or a mechanical stroboscope is satisfactory. When measuring rotational speed using a stroboscope, the stroboscope should first be set at the synchronous speed of the motor under test and then reduced until the first sharp image is achieved.
When the flash rate is set to zero and then increased, sharp images may be seen at rational intervals of the rotational speed.IEEE 114 download.IEEE 114-2001 pdf download
IEEE 114-2001 pdf download
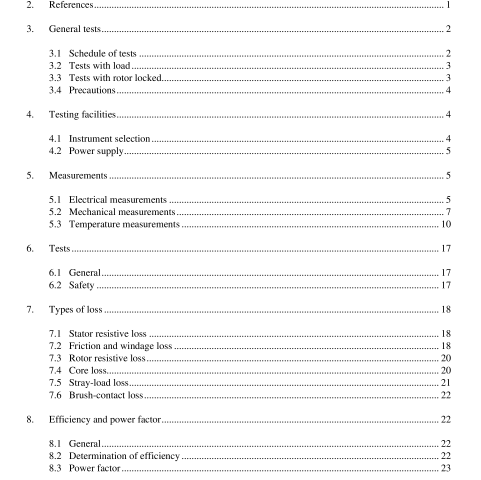
Leave a Reply