IEEE 323-2003 pdf download.IEEE Standard for Qualifying Class 1E Equipment for Nuclear Power Generating Stations
4. Principles of equipment qualification
4.1 Qualification objective
The primary objective of qualification is to demonstrate with reasonable assurance that Class 1E equipment for which a qualified life or condition has been established can perform its safety function(s) without experi- encing common-cause failures before, during, and after applicable design basis events. Class 1E equipment, with its interfaces, must meet or exceed the equipment specification requirements. This continued capability is ensured through a program that includes, but is not limited to, design control, quality control, qualifica- tion, installation, maintenance, periodic testing, and surveillance. The focus of this standard is on qualifica- tion, although it affects the other parts of the program. For equipment located in a mild environment for meeting its functional requirements during normal environ- mental conditions and anticipated operational occurrences, the requirements shall be specified in the design/ purchase specifications. A qualified life is not required for equipment located in a mild environment and which has no significant aging mechanisms. When seismic testing is used to qualify equipment located in a mild environment, pre-aging prior to the seismic tests is required only where significant aging mechanisms exist (see 6.2.1.1). A maintenance/surveillance program based on a vendor’s recommendations, which may be supplemented with operating experience, should ensure that equipment meets the specified requirements.
4.2 Qualified life and qualified condition
Degradation with time followed by exposure to environmental extremes of temperature, pressure, humidity, radiation, vibration and, if applicable, chemical spray and submergence resulting from a design basis event condition can precipitate common-cause failures of Class 1E equipment. For this reason, it is necessary to establish a qualified life for equipment with significant aging mechanisms. The qualified life determination must consider degradation of equipment capability prior to and during service. Inherent in establishing a qualified life is that a qualified condition is also established. This qualified condition is the state of degrada- tion for which successful performance during a subsequent design basis event was demonstrated.
4.3 Qualification elements
The essential elements of equipment qualification include the following:
a) Equipment specification including definition of the safety function(s)
b) Acceptance criteria
c) Description of the service conditions, including applicable design basis events and their duration
d) Qualification program plan
e) Implementation of the plan
f) Documentation demonstrating successful qualification, including maintenance activities required to maintain qualification.
The equipment user is responsible for specifying performance requirements and verifying that the documentation demonstrates that the requirements have been satisfied.
4.4 Qualification documentation The result of a qualification program shall be documented to demonstrate the equipment’s ability to perform its safety function(s) during its qualified life and applicable design basis events. The documentation shall allow verification by competent personnel, other than the qualifier, that the equipment is qualified.
5. Qualification methods
Methods for acquiring data in support of equipment qualification are listed in 5.1.1, 5.1.2, 5.1.3, and 5.1.4. Equipment is generally qualified by a combination of methods.
5.1 Initial qualification
5.1.1 Type testing
A type test subjects a representative sample of equipment, including interfaces, to a series of tests, simulating the effects of significant aging mechanisms during normal operation. The sample is subsequently subjected to design basis event testing that simulates and thereby establishes the tested configuration for installed equipment service, including mounting, orientation, interfaces, conduit sealing, and expected environments. A successful type test demonstrates that the equipment can perform the intended safety function(s) for the required operating time before, during, and/or following the design basis event, as appropriate.
5.1.2 Operating experience
Performance data from equipment of similar design that has successfully operated under known service con- ditions may be used in qualifying other equipment to equal or less severe conditions. Applicability of this data depends on the adequacy of documentation establishing past service conditions, equipment perfor- mance, and similarity against the equipment to be qualified and upon which operating experience exists. A demonstration of required operability during applicable design basis event(s) shall be included in equipment qualification programs based on operating experience, when design basis event qualification is required.
5.1.3 Analysis
Qualification by analysis requires a logical assessment or a valid mathematical model of the equipment to be qualified. The bases for analysis typically include physical laws of nature, results of test data, operating experience, and condition indicators. Analysis of data and tests for material properties, equipment rating, and environmental tolerance can be used to demonstrate qualification. However, analysis alone cannot be used to demonstrate qualification.IEEE 323 pdf download.IEEE 323-2003 pdf download
IEEE 323-2003 pdf download
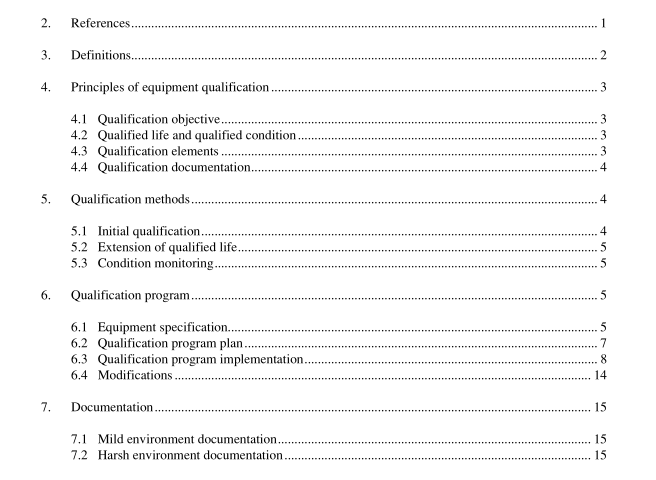
Leave a Reply