IEEE 841-2009 pdf download.IEEE Standard for Petroleum and Chemical Industry—Premium- Efficiency, Severe-Duty, Totally Enclosed Fan-Cooled (TEFC) Squirrel Cage Induction Motors—Up to and Including 370 W (500 hp)
4. Ratings
4.1 Basis of rating
Motors shall be rated on a continuous-duty basis. The output rating shall be expressed in power available at
the shaft at the specified speed, frequency, and voltage.
NOTE—Motors should be applied within their rating based on a service factor of 1.0. In applications requiring a prolonged overload capacity, the use of a higher power rating is recommended to avoid the reduction of sulation and
bearing life associated with operation above the 1.0 service factor.
4.2 Frame assignments
To the extent applicable, motors shall comply with the frame size assignments of NEMA MG 1-2006,Part 13.
4.3 Voltage and frequency ratings
The standard voltage ratings for 60 Hz 3 phase are 200 V, 230 V, 460 V, 575 V, 2300 V, and 4000 V. Dual oltage motors are acceptable only for 2300 V and 4000 V ratings. Voltage ratings for 50 Hz 3 phase are 230 V, 400 V, 690 V, and 3300 V.
NOTE—It is not practical to build induction motors of all ratings at all of these voltages.
4.4 Synchronous speed ratings
Synchronous speed ratings at 60 Hz are 3600 r/min, 1800 r/min, 1200 r/min, or 900 r/min.
Synchronous speed ratings at 50 Hz are 3000 r/min, 1500 r/min, 1000 r/min or 750 r/min.
4.5 Enclosures Enclosures shall be TEFC or totally enclosed non-ventilated (TENV) and shall have a degree of protection of IP 55. If replaceable shaft seals are used to achieve this degree of protection, they shall be the noncontact or noncontacting-while-rotating type with a minimum expected seal life of 5 years under usual service conditions. Degrees of protection are defined in NEMA MG 1-2006, Part 5.3 Drain fitting holes are permitted to be plugged during the enclosure IP 55 ingress test.
5. Electrical performance
5.1 General Unless otherwise specified in this standard, motor electrical performance and characteristics shall be in accordance with NEMA MG 1-2006.
5.2 Motor designs and starting characteristics Motors shall have Design B torque/current characteristics and starting capability as defined in NEMA MG 1-2006, Part 12. Where power and speed ratings fall outside Part 12, characteristics and capabilities shall meet or exceed the specifications defined in NEMA MG 1- 2006, Part 20.
5.3 Power supply variations
5.3.1 Sine wave supply voltage
a) Motors shall operate successfully under running conditions at rated load with variation in the voltage or frequency not exceeding the following conditions:
1) ±10% of rated voltage, with rated frequency
2) ±5% of rated frequency, with rated voltage
3) Combination of voltage and frequency variation of 10% (sum of absolute values) of the rated values, provided that the frequency variation does not exceed ±5% of rated frequency
NOTE—For the effects of voltage, voltage unbalance, and frequency on motor performance, see Sections 14.30 through 14.36 of NEMA MG 1- 2006.
b) Motors shall operate successfully under running conditions at rated load and frequency when the voltage unbalance at the motor terminals does not exceed 1%. For voltage unbalance greater than 1%, the motor shall be derated in accordance with Section 14.36 of NEMA MG 1-2006
5.3.2 Adjustable speed drive (ASD) Supply When the motors supplied under this standard are to be applied on a nonsinusoidal source and/or an adjustable speed application, the manufacturer should be consulted to determine whether the motor will operate successfully over the required speed range. Refer to NEMA MG 1-2006, Part 30 and 31. Proper selection of the motor and drive is required to avoid the following conditions:
a) Motor current (rms) exceeding the continuous sinusoidal nameplate rating due to excessive voltage harmonics or improper volt/hertz levels
b) Excessive winding temperature due to insufficient cooling, excessive torque levels, or improper volt/hertz levels; and increased losses due to harmonics
c) Insufficient motor accelerating torque at reduced speeds due to insufficient volt/hertz levels or limitations in the drive’s momentary current capacity
d) Increased noise levels due to increased fan noise (above base speed), excitation of mechanical resonances, and/or magnetic noise caused by supply source harmonics
e) Mechanical failure of the motor or coupling due to torque pulsations, operation at or near mechanical resonances, or excess speed
f) Winding failures due to repetitive high-amplitude voltage spikes created by the carrier frequency of the drive fast switching transients and the motor feeder cable system
g) Damage to the motor and drive due to improper application of power factor correction capacitors or harmonic filters.IEEE 841 pdf download.IEEE 841-2009 pdf download
IEEE 841-2009 pdf download
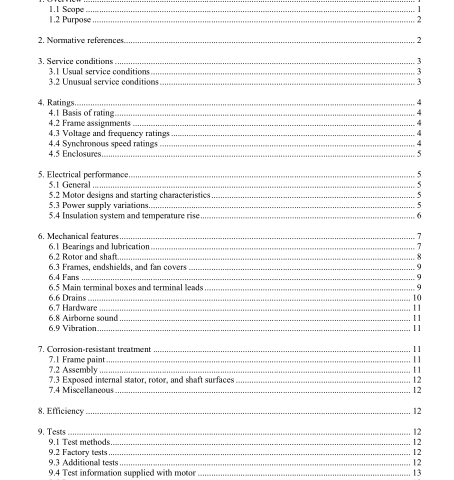
Leave a Reply